The demands on procurement managers in the field of mechanical engineering are higher today than ever before. They face growing competition, high raw material and production costs, as well as ever-evolving requirements.
Procurement managers typically oversee a machinery fleet comprised of a variety of machines, each consisting of different components. The management, maintenance, and improvement of these machines require a high level of expertise and often entail a growing annual budget.
We would like to share the impressive success story of a procurement manager who approached us a few months ago. His challenge was to increase the production capacity of his facilities, minimize downtime, simplify assembly processes, and simultaneously reduce costs.
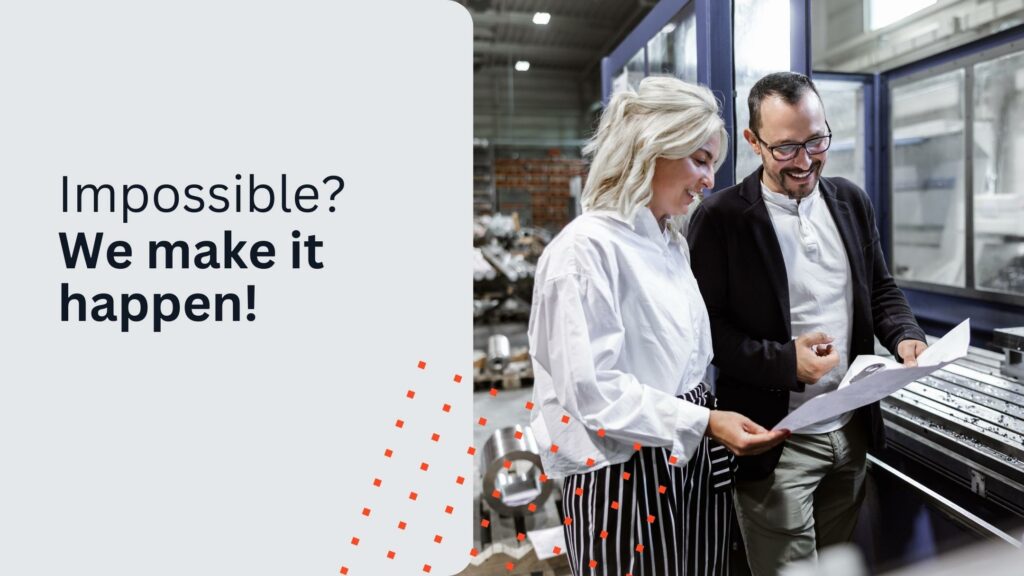
It might sound almost utopian, doesn’t it? Not for us!
Let us explain how we managed to reduce 15% of the manufacturing costs of the entire machinery.
Step 1: Analysis
The first step involved a thorough examination of the existing machinery fleet. Particular attention was given to the use of hydraulic cylinders in mechanical engineering. These components are of paramount importance as they generate and control mechanical forces. Thanks to their high performance, durability, and precision, hydraulic cylinders are indispensable in today’s industry.
Various cylinders with similar but non-standardized specifications were in use within our customer’s machinery systems. This led to high manufacturing costs for different hydraulic cylinders as well as redundant expenses for documentation and spare parts.
For the potential analysis of these systems, we employed a unique method to identify cross-system standardization potential by combining expert knowledge, data-driven analysis, and artificial intelligence.
Together with the procurement manager, we analyzed the following specifications:
- Cylinder drawings
- Requirements (operating pressure, environmental factors, stroke, etc.)
- Number of variants
- Environmental parameters
- Technical requirements
- Installation spaces
- Lifecycles
- Maintenance friendliness (accessibility)
Step 2: Standardization
Once the requirements were clarified, we designed hydraulic cylinders that could be used in a versatile manner. These cylinders could be produced in larger quantities, significantly reducing manufacturing costs. Simultaneously, the assembly of the cylinders was simplified, and the additional costs for documentation and spare parts were eliminated.
Overall, by standardizing the hydraulic components, not only were the processes streamlined, but machine costs were also reduced.
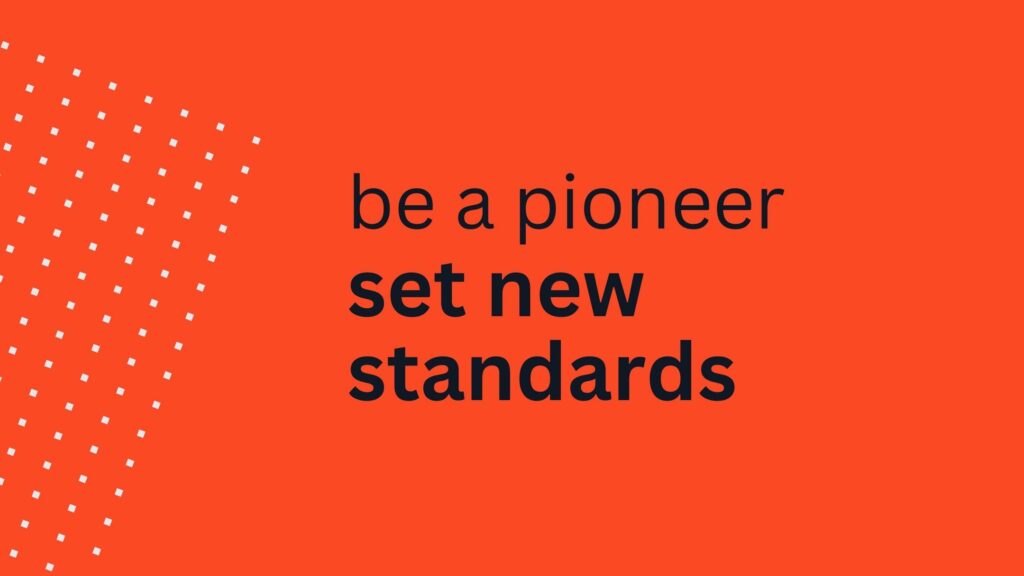
Unbeatable result: Through the standardization of hydraulic cylinders, not only were the cylinder costs reduced, but the overall manufacturing costs were lowered by 15%.
Be a pioneer and set new standards. Harness the benefits of efficiency improvement through targeted standardization. What challenges are you currently facing with your machinery or processes? We would be happy to discuss the possibilities for efficiency improvement and cost reduction in your machinery manufacturing. Save future manufacturing costs through strategic standardization and maximize your efficiency.